Firstly, as I noted in my post on the Congressional Hearings there is a good Primer now available on the Web that contains a lot of the information (including the chemical composition of some of the fracing fluids) that people are concerned to get. Also, (h/t to Jane Van Ryan of API) there is a video which explains the process. Neither, however, explains that the wells typically have a relatively short life, with around 60% of well production coming that first year, a point I have posted on earlier.
To begin with it’s probably best to start with rock pressure. And to explain this I am going to do some simplification, so, as I ask in most of these “techie talks”, to those who do know better please understand that this is trying to explain concepts, but also please do comment on where I may either accidentally or by error, get something wrong.
As we go deeper into the earth, the weight of the ground above us will also increase. For a very simple measure we can assume that this is around a 1 pound per square inch (psi) increase for every foot deeper we go. So if we were, for example, 10,000 ft down then the pressure in the rock due to that weight would, undisturbed, be around 10,000 psi. (This is about 7 times the pressure that you see coming out of a car wash pressure washer for example).
When a oilwell is drilled vertically down into that rock it does not see this pressure, but it does see a part of it. The reason is that the rock on either side of the hole can now expand into the hole, and we’d rather it didn’t. (It’s somewhat as though you step on a rubber eraser – the eraser will bulge out laterally as it compresses vertically under your weight). The resistant pressure in the horizontal direction can be calculated as a function of the vertical pressure through a ratio known as Poisson’s Ratio . Sufficient for our discussion to say that can have a value of about 0.3. So that if we are 10,000 ft down, then the vertical pressure on the rock will be around 10,000 psi, and the horizontal pressure will be around 3,000 psi. If the well is vertical then the casing for the well has to be designed for the 3,000 psi level.
Now, if instead of just drilling the well vertically I turned and drilled it out horizontally through the rock, then the hole would now have the 10,000 psi squeezing down vertically, and the 3,000 psi coming in from the side. So the first thought that we have is that the casing (the lining that we put into the hole to make sure that it stays open) has to be a bit stronger. Life gets, however, a bit more complicated than that. When you put a hole into ground that is under pressure, the first response of the rock is to try and move the weight of the rock over the hole onto the rock on the sides of the hole. This roughly doubles the pressure that is on that thin layer. Before the hole was put there that particular rock was held in place by the rock around it, and collectively the mass could carry the original pressure. But now there is no rock where the hole is, and thus the confining pressure on the rock there is less. (In technical terms you have shifted the load from a triaxial confinement under 10,000 psi to a uniaxial load of 20,000 psi.) The result can be that the rock on the sides of the hole crushes under the load. This then puts crushed rock or sand into the hole, and that interferes with lots of things. Now you can possibly stop that by keeping the pressure high in the liquid that you are using inside the hole to get the drilled rock out (the drilling mud), but if you keep that pressure too high, then the oil/gas won’t flow to the well and so you have to drop it down to a certain level.
Life also gets a bit more complicated in reality, since the presence of the fluid in the rock tends to even out the pressure within it. So that while, relatively close to the surface, and in a dry rock the ratios may be as I gave them earlier, with a fluid saturated rock, and in an over-pressured region, the horizontal pressure can be as high as 80% or more of the vertical value. The values generally get closer to 100% as the wells go even deeper, but that is another story.
So rock pressure is the first problem that you have to deal with. But why do we drill the horizontal holes in the first place, why can’t we just use the old vertical ones. Well the reason is that the old ones didn’t work very well. And to explain that I am gong to try and re-explain a recent article from Penn State . (then I’ll give the relevant quote).
Shale is a very fine grained rock, and though gas can gather in the small pores of its structure, if the gas is to flow to a well, then it has to migrate through passages that are very narrow, and thus very resistive to that flow. However, as the shale has been formed under geological pressure and over time, the pressures not only compressed it from mud into shale, but they also caused it to fracture. In the Marcellus shale, for example, the cracks that occurred in the shale are roughly vertical, and form two sets that are perpendicular to one another.
The first advantage that a horizontal well has, over a vertical one, is that the well can penetrate a long way through the rock that carries the oil or gas (OG). The amount of OG that comes from the rock is, in part, a function of how long the length of well is in the rock that carries it. So that while a vertical well might produce say 800 bd from a well that goes straight through a 200 ft thick layer of oil-bearing rock, when the well is drilled so that it goes out 4 miles horizontally through the oil-bearing rock, then the production per day may go up to 10,000 barrels.
The second advantage relates to the way in which the fractures lie in the rock. Because they are vertical, a vertical well won’t hit very many of them, and so since these fractures provide an easy flow of OG to the well, rather than the difficult path through just the rock, then the well will not show very much production. (And this was the case with many of these shales when tested earlier).
However if the well is horizontal (see figure) then the well will intersect many of these fractures and in drawing the fluid from them will also provide an easy path for fluid to ease out of the rock into the fracture paths, so that the entire rock can be more easily drained.
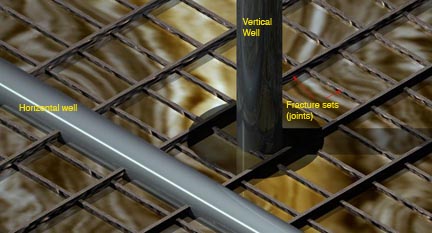
Now in the picture I have shown one set of joints as being bigger than the other. And that is usually the case, because the horizontal pressure, that earlier I had suggested was the same in each direction, actually usually isn’t. The strongest horizontal pressure will tend to close up those fractures that run perpendicular to it, and tend to open the ones that run parallel with it. Thus it helps to know at the level of the shale, what the pressures in the different directions are (those engineering among us generally refer to them as stresses rather than pressures). The best direction to drill is then perpendicular to the maximum horizontal pressure, if we want to take the best advantage of the fractures in the rock. The only problem with this is that it also increases the pressures on the sides of the borehole, so that if we go that way, and the rock is not that strong, then we may be making the borehole stability worse.
But even with a horizontal well the production may not be that great, because the fractures are still relatively narrow, and so flow won’t be that fast. And so there is another tool that can be used, and that is to deliberately put a crack into the rock on the side of the borehole. On a very small scale, if you look at the picture, you can see a shaded zone around the vertical well. If I could make a crack out from the well at that level and grow it out just a short way you can see that it already intersects two of the better joint sets, whereas at the beginning the well didn’t reach any. And if we could do this from the horizontal well and grow that crack out a goodly distance horizontally, then it would intersect a lot of the vertical fractures and production would become high and useful.
There are, however, three snags to forming and growing that crack, all solvable, but all costing additional money. The first is that if we just grow the crack out and then let the weight of the overlying rock close it up again, then we haven’t made a whole lot of difference. So we have to prop the crack open. For this we need to inject relatively fine grained particles (let’s call it sand, though the technical term is proppant) into the crack in enough quantity that it will fill up the crack and hold it open so that it gives an easy path through the rock to the well for the OG. (We won’t go into what a mess pumping sand at more than 10,000 psi makes of the pump – Halliburton gets paid very nicely to fix those problems).
The second snag is that trying to push sand into a thin crack and get it to go very far can be an exercise in futility. Among other things if you are using plain water the sand tends to settle to the bottom rather fast, and if it fills the crack near the well, it then acts as a filter to stop sand going back further into the slot. So now we change the chemistry of the water by adding what are usually known as long-chain polymers. These chemicals thicken the water so that it will (at relatively low chemical percentages) suspend the sand in the fluid. Because these molecules are also slippery (in another variety they are added to the water in crowd control water cannons to produce what is known as Banana Water – since it makes the street too slippery to stand on) they also reduce the friction between the fluid flow and the walls of the crack, and this also helps carry the sand further back into the crack, and gives the slickwater title to the hydrofrac.
The third snag is a bit more technical. You remember that earlier on I talked about the pressure about the hole causing the sides of the horizontal well to crush. Well at the top and bottom of the well instead of the rock seeing this additional crushing pressure, the shifting of the vertical load to the walls of the hole, can mean that the rock will go into tension, where it is much weaker. As a result cracks can appear in the top and bottom of the horizontal hole. Why is this a problem? Because the easy way to cause a fracture to grow is to fill the well with liquid and increase the pressure of the liquid until the rock breaks. (Hence hydraulic fracture or hydrofrac). But if there is a crack there already then just increasing the pressure in the hole causes that crack to grow. And if the crack is vertical then it won’t grow in the horizontal direction we want. And so it is time to call in the engineers (who also don’t come cheap) to do the interesting things that cause the crack to grow in the right direction.
The benefits to all this for the Marcellus has been described by Engelder.
"Conservatively, we generally only consider 10 percent of gas in place as a potential resource," said Engelder. "The key, of course, is that the Marcellus is more easily produced by horizontal drilling across fractures, and until recently, gas production companies seemed unaware of the presence of the natural fractures necessary for magnifying the success of horizontal drilling in the Marcellus." The U.S. currently produces roughly 30 trillion cubic feet of gas a year, and these numbers are dropping. According to Engelder, the technology exists to recover 50 trillion cubic feet of gas from the Marcellus, thus keeping the U.S. production up. If this recovery is realized, the Marcellus reservoir would be considered a Super Giant gas field. . . . . These fractures, referred to as J1 fractures by Engelder and Lash, run as slices from the northeast to the southwest in the Marcellus shale and are fairly close together. While a vertical well may cross one of these fractures and other less productive fractures, a horizontally drilled well aimed to the north northwest will cross a series of very productive J1 fractures.
You can see examples of the fracture patterns in the Marcellus here
The upfront money may give some pause to prospectors. A typical well that drills straight down to a depth of about 2,000 to 3,000 feet costs roughly $800,000.
But in the Marcellus Shale, Range and other companies hope a different kind of drilling might yield better results — one in which a well is dug straight down to depths of about 6,000 feet or more, before making a right angle to drill horizontally into the shale. That kind of well could cost a company $3 million to build, not counting the cost of leasing the land, Engelder said.
The company, in a December financial report, estimated that two horizontal wells are producing roughly 4.6 million cubic feet of gas per day. Tests on an additional three recently completed horizontal wells showed potential for a total of 12.7 million cubic feet of gas per day. Industry experts call those results promising.
The benefits have also been projected here.And while they may be considerable, it is only after the wells are in production, and not only initial flows, but also well lifetimes are established, that the true benefit will become apparent.
But until some solid, repeatable well data emerges, the Haynesville will remain more diamond in the rough than diamond ring. As BMO Capital Markets analyst Dan McSpirit rightly noted in a report last week: "The proof (of Haynesville economics) is in how the wells get drilled and the rates of return such operations yield." He added, "These are early innings. Lasting value creation should be revealed later in the game.".
So there you have a brief explanation of how the new technology is slowing, though it won’t stop, the declining gas reserve in the United States,
.
An earthquake is the result of a sudden release of energy in the Earth's crust that creates seismic waves. The seismicity or seismic activity of an area refers to the frequency, type and size of earthquakes experienced over a period of time. Earthquakes are measured using observations from seismometers. The moment magnitude is the most common scale on which earthquakes larger than approximately 5 are reported for the entire globe.discount sexy lingerieSwingers Sydney
ReplyDeleteThis comment has been removed by the author.
ReplyDeletehot girl | hot girl | cute girl | girl xinh | funny |
ReplyDeletetravel vietnam | visit vietnam | funny picture | funny picture
socks proxy | socks5 | proxy | proxy free
Nice blog - I enjoyed the technical content.
ReplyDeletehttp://www.water-research.net
dia chi hoc ke toan tai cau giay
ReplyDeletedia chi hoc ke toan tai ha dong
dia chi hoc ke toan tai bac ninh
trung tam dao tao ke toan tai ha dong
trung tam dao tao ke toan tai cầu giấy
trung tam dao tao ke toan tai thanh xuan
trung tam dao tao ke toan tai tphcm
khóa học kế toán tổng hợp tại hải phòng
khóa học kế toán tổng hợp tại tại bắc ninh
khóa học kế toán tổng hợp tại tphcm
khóa học kế toán tổng hợp tại hà nội
trung tam dao tao ke toan tai quan 3
trung tam dao tao ke toan tai binh duong
trung tam dao tao ke toan tai bac ninh
trung tam dao tao ke toan tai hai phong